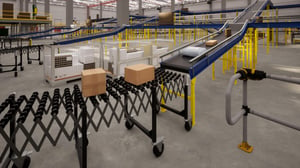
The Value of Human Capital as Automation Gains Momentum in Modern Warehouses
There is no question that the growing concept of automation is permeating multiple business sectors, especially the material handling industry. In the current state of technological advancements, the prevailing value of human capital remains integral to industry success as automation gains momentum in modern warehouses.
Configura Doubles Down on the Material Handling Industry
Configura, with support from Dynata, collected material handling industry (MHI) data across the three markets we operate in: Japan, Germany and the United States. After analyzing the responses of the nearly 700 MHI employees about upcoming innovations in the field, 41.7 percent responded that warehouse automation will be the most common and productivity-boosting innovation over the next five to 10 years. While automation continues to become increasingly relevant, it is critical for the entire material handling sector to understand where human employees fit in this new era.
One surprising data point in our research stands out among the rest. When asked about the most crucial asset involved in warehouse design and operations, 26 percent of respondents reported the number of human workers on the warehouse floor—the highest response by far.
Which begs the question: with automation becoming increasingly prevalent in warehouses, what will the integration of human workers and robotics look like in the next year, five years and beyond? And, with the data showing automation is on the mind of most decision-makers, why (and for a good reason) and how are human workers being considered a highly critical aspect of warehouse designs and operations?
Human-less Warehouses Not Yet Achieved—Maybe, Never?
Presently, automation and robotics do not fully facilitate human-less warehouses. For example, machines break or malfunction, which requires maintenance, and central control systems are still best overseen by humans versus Artificial Intelligence (AI) or highly skilled software.
While automation and robotics help facilitate the movement of materials within warehouses, the humans working alongside machines are still vital for maintaining daily operations and other tasks robots cannot currently perform.
In the future, advancements in technology, software and AI may lead to fully automated warehouses managed via off-site control centers. However, these technologies will still rely heavily on human involvement for productivity and quality assurance. Because of the need for human support, further integrating automated and semi-automated robotics and digital technologies in warehouse spaces will increase the need for human capital in the short term.
Automation and robotics tools can support the work of humans, eliminating tedious labor practices and allowing people to spend more time on complex problems and tasks. Under the industry’s current circumstances—including an industry-wide labor shortage—more skilled workers will be needed for order fulfillment as volumes increase.
The Need for High-Quality Training to Contend with Evolving Roles
The working relationship between human beings and robotics in the material handling industry is creating an era of rapid change. As technology advances and becomes integrated into warehouses, the role of the human worker must evolve.
In Configura’s survey, more than half of all respondents identified consistent worker training as the most important facet of automation and worker integration. In short, understanding how the function of human workers will change and being best prepared to fulfill their new function should be the highest priority for warehouse managers and business owners.
Whether consistent worker training comes in the form of in-person or digital learning, accessibility will be critical to ensure that effective instruction prepares employees to work in highly automated environments.
While humans are working in tandem with robotics, adequate training is needed to ensure safety as well as productivity. If quality training isn’t achieved, significant consequences are likely to occur—i.e., increasing accidents, injury and loss of productivity. For these reasons, the promise of automation may lose some appeal.
With Power Comes Responsibility to People
The material handling industry is rapidly moving toward the greater use of automation and digital tools. To find the most success, those in the material handling industry need to be prepared to help their human workforce understand the new roles asked of them.
People are essential in warehouse operations—and when strategically connected to automation and robotics, harmony can occur. For that reason, high-quality and consistent worker training is vital to ensure productivity, safety and ease of work in modern warehouse spaces today and in the future.
Additional findings from Configura’s MHI research will be made available in the coming months.
Subscribe to the Configura Blog to get notified whenever we post something new:
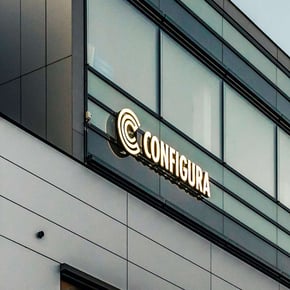