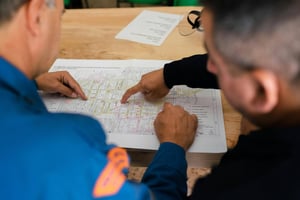
The High Costs of Early vs Late Stage Errors in Material Handling
Accuracy is Key: Why Small Mistakes Can Have Big Consequences in Your Warehouse
In the fast-paced world of material handling, even minor errors can create significant financial and operational setbacks. From warehouse layout planning to final implementation, every detail matters. Small miscalculations or overlooked inefficiencies can snowball into costly disruptions, affecting productivity, increasing operational costs, and even compromising customer satisfaction.
The Cost of Inaccuracy
At the heart of every successful material handling project lies accurate data. Whether designing a new warehouse, optimizing existing storage solutions, or integrating automation, precise measurements and validated information are essential for efficiency and cost-effectiveness.
When errors creep into the process—whether through incorrect dimensions, miscalculated load capacities, or poor workflow planning—the repercussions can be far-reaching. Some of the most common consequences include:
- Increased costs – Errors can lead to expensive rework, material waste, and unplanned modifications.
- Operational inefficiencies – Poor planning can result in workflow bottlenecks, reduced throughput, and unnecessary downtime.
- Safety risks – Incorrect equipment specifications or improper layouts may pose hazards for workers.
- Customer dissatisfaction – Shipping delays and inventory errors can erode customer trust and damage a company’s reputation.
Complex material handling systems require precise planning and accurate data to avoid costly errors.
Early-Stage Errors: The Ripple Effect
A mistake made during the initial design phase may seem minor, but the effects can compound over time. For example, miscalculating storage capacity could result in overcrowded aisles, restricting forklift movement and slowing down order fulfillment. Likewise, overlooking workflow optimization could create unnecessary congestion points, forcing warehouse staff to take inefficient routes.
Top 3 Ways to Prevent Early-Stage Errors in Material HandlingTo mitigate these risks, consider these essential strategies:
|
While errors at this stage are easier to correct, they still come at a cost. Redesigning layouts or modifying plans mid-way through a project can delay implementation and require additional resources. However, when identified early, these errors are far less damaging than if they remain unnoticed until later stages.
Late-Stage Errors: A Financial Earthquake
The impact of mistakes grows exponentially when discovered during the construction, installation, or operational phases. Unlike early-stage errors, late-stage mistakes often require expensive modifications, such as tearing down newly built structures, reordering materials, or even purchasing new equipment.
Consider a scenario where a design flaw in a conveyor system is only discovered once installation has begun. At this stage, adjusting the design could require not just additional costs, but also weeks of downtime—delaying shipments and directly impacting revenue. Worse, if an oversight leads to incompatible automation systems, the cost of reconfiguring the entire setup could far outweigh the original project budget.
The consequences of late-stage errors can include:
- Escalated costs – Emergency fixes, rush orders for new materials, and increased labor hours.
- Severe project delays – Timeline setbacks that disrupt business operations and logistics.
- Reputation damage – Late deliveries and operational failures that harm relationships with clients.
The Risk of Suboptimal Software
Many of these costly mistakes stem from using outdated or suboptimal design and planning tools. Relying on manual data entry, static spreadsheets, or limited visualization software increases the risk of human error and missed details.
Common issues caused by inadequate software include:
- Limited visualization capabilities – Without detailed 3D modeling, critical layout flaws may go unnoticed.
- Inaccurate data analysis – Poor analytics tools can lead to incorrect inventory forecasts or inefficient storage solutions.
- Lack of system integration – Disconnected software solutions can create communication gaps, leading to misaligned logistics and delays.
In contrast, modern material handling software solutions provide real-time design validation, automated error detection, and seamless integration with warehouse management systems (WMS) to minimize risks and maximize efficiency.
Avoiding Errors with Automatic Clash Detection and Optimal Path Creation in CET Material Handling
Protect Your Projects, Protect Your Profits
By implementing best practices and investing in the right software and data-driven decision-making, you can significantly reduce the likelihood of costly errors and ensure smooth, efficient warehouse operations.
Key Takeaways:
- Accurate data is essential for successful warehouse planning and operations.
- Early-stage errors are easier to correct but can still impact project timelines.
- Late-stage errors can result in massive financial losses and operational disruptions.
- Using advanced software helps detect and prevent errors before they escalate.
- Collaboration and quality control are crucial for ensuring data integrity and preventing mistakes.
In material handling, small mistakes can lead to big consequences—but with the right tools and proactive strategies, you can safeguard your business from unnecessary risks.
Subscribe to our blog to stay updated on the latest trends and best practices in material handling.
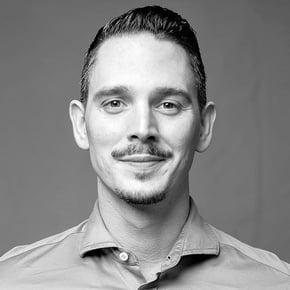